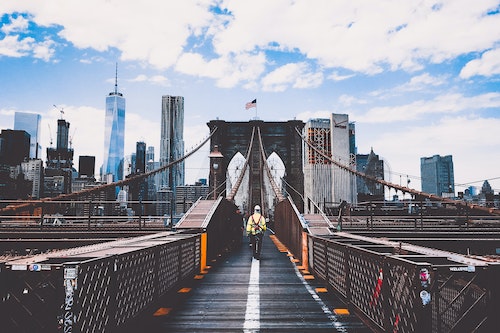
What Is Predictive vs Proactive Maintenance?
In the industrial world, the methods used to maintain machinery or equipment are essential for the safety of workers, while also ensuring the reliability and longevity of the unit and its components. When it comes to maintenance, there are two main approaches businesses take; predictive, and proactive. Understanding the differences between predictive versus proactive maintenance and how they can help you realize significant long-term cost savings and reliability can be beneficial when planning your maintenance scheduling.
Predictive Maintenance
Predictive maintenance (abbreviated as PdM) is all about watching for signs of deterioration to accurately determine when an item or product should be serviced or replaced. The goal of predictive maintenance is to avoid the failure of machinery before it happens by regularly monitoring the condition of the equipment and its components. This method is usually more cost-effective for businesses in comparison to reactive approaches.
This approach requires a high level of expertise from personnel – such as engineers, technicians, or specialists – as its implementation requires them to have a deeper understanding of the particular working mechanism of the equipment and its components. Predictive maintenance thus depends heavily on the analytics and insight these professionals can bring to the table.
Predictive maintenance is typically implemented in connection with Data Loggers or Continuous Monitoring Technologies. Common examples include vibration analysis and thermography, ultrasound measurements, current signature analysis, oil and fluid analysis, and online particle analysis. Using these tools help in monitoring machinery’s vibrations, temperatures, and other relevant data points to help detect any potential issues early on.
Proactive Maintenance
On the other hand, Proactive Maintenance is a form of planned maintenance. It consists in predicting what particular pieces of the machinery might require repair or the replacement of the parts to keep the machines in optimal condition. With the help of a maintenance scheduling system, technicians can anticipate maintenance requirements and plan for them in advance.
In terms of setting up proactive maintenance, businesses can create their own schedules based on their data, or use commercial-off-the-shelf products to provide advice on the maintenance. This approach has the advantage of reducing potential downtime with machines by identifying potential problems ahead of time before they occur so repairs and replacements can be completed before they negatively affect the machine or its output.
What’s more, with proactive maintenance, monitoring data points from equipment in real-time gives a business more control as to when and where resources should be deployed to provide maintenance. Thus, this helps save money by reducing down-time for repairs and avoiding possible losses such as customers’ dissatisfaction due to output being affected.
Advantages Of Predictive vs Proactive Maintenance
When it comes to the advantages of setting up a predictive and a proactive maintenance system, one of the biggest advantages is cost savings. As mentioned earlier, predictive maintenance helps businesses significantly reduce expensive visits from technicians to analyze a faulty unit during repairs. With proactive maintenance, businesses are better prepared with plans to take active steps that can help fill the gap in the equipment life cycle.